Moventas Ltd.
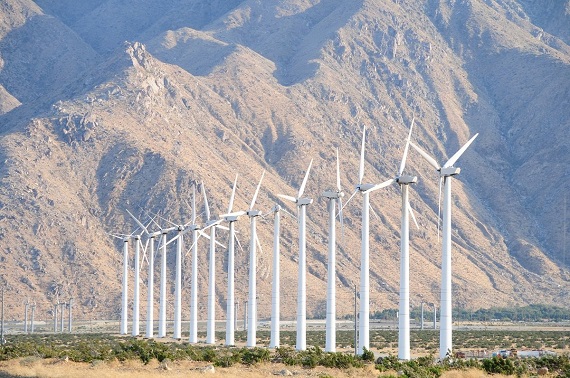
When we say field-proven, we mean it. We have always been able to offer the wind industry the most innovative, competitive technology in all onshore platforms; from kilowatt to multi-megawatt products. In the MMW class alone we have units that have been in operation since 2004.
Highly optimized structures lead to low cost of energy for the wind power industry. This has been the leading idea of Moventas’ design work since 1980's. Especially today, the renewable energy industry's race for grid parity is what we base our design on.
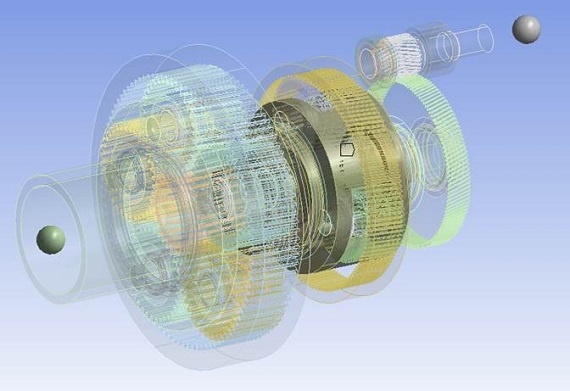
Cost reduction of a drivetrain is a significant factor when designing new power line platforms for wind turbine generators. Therefore new technologies must be introduced to respond the request coming from the market. Moventas has foreseen this development and developed a concept that enables new kind of cost efficiency throughout the drivetrain value chain.
Lighter structure & Better torque density
• Remarkable product mass savings.
• Increased number of planet wheels at input stage decreases complete gear dimensions significantly.
• Highly optimized casted components and new material selections that lead to cost effective overall structure.
• No critical effects against known failure modes.
• Better serviceability; enables up-tower repair.
Revolutionary design without reliability compromises
• Increased number of planetary wheels at input stage.
• Design dimension rules updated.
• Component material changes.
• ME material is used on planet wheel and sun shaft.
• New design methods are used, however technical & reliability requirements not compromised.
• High torque carrying capacity for existing and future rotor diameters.
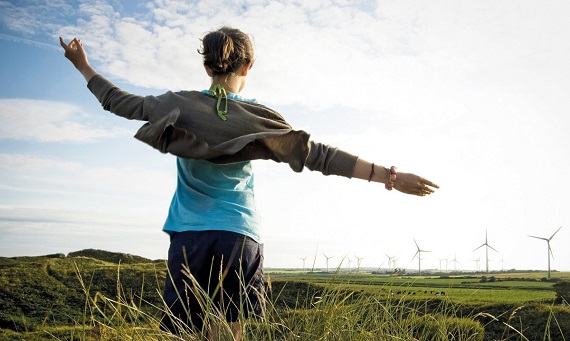
Power Density
In the constant pursuit of reducing the overall weight of the wind turbine mass, Moventas' engineers have discovered an innovative power / density concept based on proven designs. By designing it compact and extremely lightweight, our state-of-the-art gearbox provides a significant reduction of tower head mass. The need for drivetrain space in the axial direction is equally reduced by the power density concept. All reaction forces can be transmitted to the nacelle structure in an optimal way. The concept also ensures that there is no need for separate support structures for the generator.
Torque density is used to measure gear performance. It states the level of torque one kilogram of material, used for gear unit, can carry. Lowering the mass influences also to gear dimension, so density correlates with mass. Moventas' expert gear design skills and application know-how with improved materials allow higher gear torque density for new gear unit designs.
Noise & Vibration
Moventas has successfully reduced the noise level of its gearboxes by improving tooth accuracy and choosing the optimal geometry and profile. Theoretical evaluation as well as on-site testing is used to eliminate any harmful resonance sounds of the structural elements. To achieve noiseless wind power, the gear unit must not vibrate. Therefore, our gear units are especially designed to prevent vibrations from passing through the gearbox fixing points to the foundation of the wind power plant.
Verification
The Moventas product portfolio is the result of proven technology including modular components for all drivetrain solutions. Moventas planetary gear consists of our special knowhow of e.g. integrated bearings, case hardened ring wheels and Flexspider technology. Our product concepts are based on approved methods of regulatory agencies.
All the gear units are verified by tests and measurements. Moventas has vast experience from prototype testing and qualification. During the last decade we have performed over one hundred modern wind turbine gear prototype test in MW class alone. Typically prototype gear units go through lifecycle and cold climate chamber tests. We also use virtual prototype environment to define drivetrain dynamics.
See how Moventas products' torque density has developed over the years!
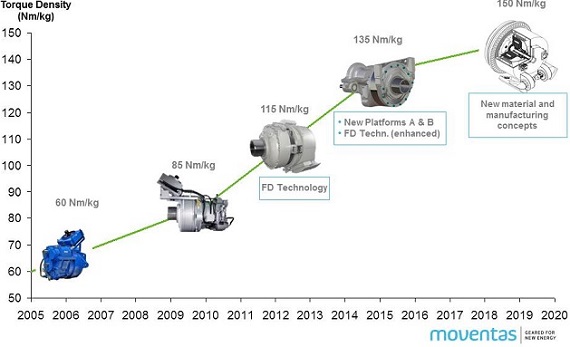
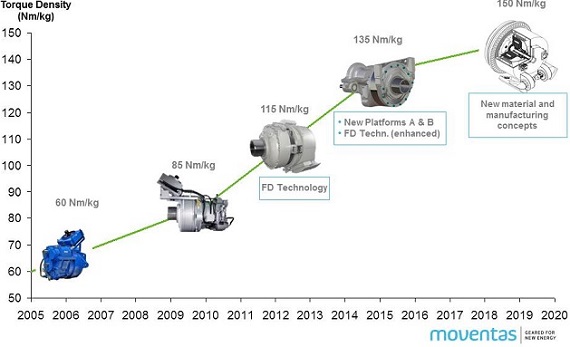
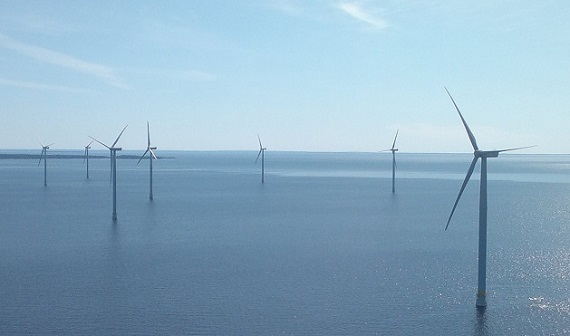
Offshore requires optimum reliability and ease of maintenance.
In developing offshore wind turbine gears, we do not only cut the cost of energy by reducing the capital cost and weight of the drivetrain, but also minimize the lifetime cost of machinery by improved performance and maintenance made easy.
Moventas currently designs and manufactures offshore in the 7-8 MW power class for e.g. Samsung Heavy Industries.
Key Benefits
• High-grade materials and innovative technology
• Case hardened ring wheel
• Enables low O&M Costs
• Remote diagnostics system CMaS guarantees O&M peace of mind.
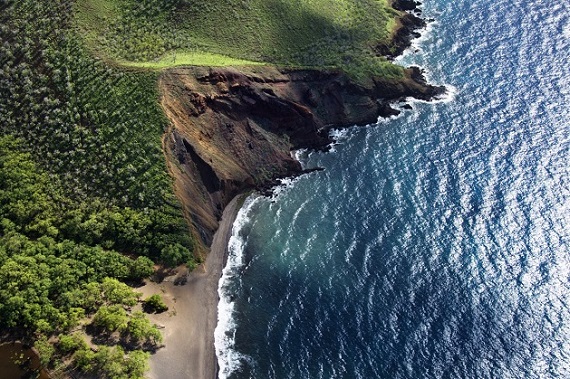
Combining our ideal wind and marine background into innovation.
With over 70 years of experience in industrial and marine gear applications and with a further 35 in wind turbine gearbox manufacture it is no surprise that Moventas is already working closely with marine tidal turbine OEMs.
Our open and innovative approach to customer needs combined with our pro-active R&D philosophy sets us apart from the competition. Our attention to detail, quality and serviceability is well known throughout industry as is our total lifecycle support services.
We design custom made tidal gearboxes according to customer needs, representing the Moventas quality and reliability that's well known in the wind industry and emphasizing easy serviceability and lifecycle care.
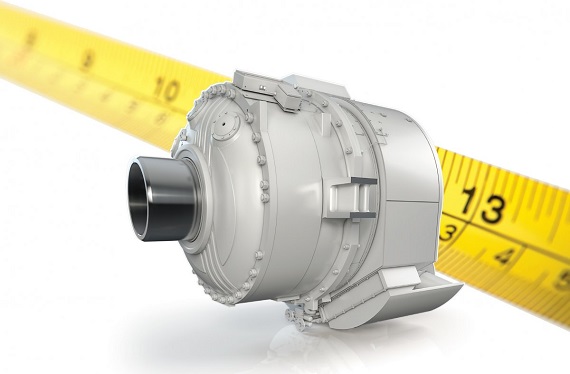
The industry’s smallest and most light-weight gear and generator combination.
Moventas has combined its latest gear solution with the proven medium-speed permanent magnet generator (PMG) of The Switch, a leading supplier of megawatt-class permanent magnet generator and full-power converter packages. The result is a solution that offers high availability, compact size and lowest weight: the FusionDrive®.
FusionDrive reduces CoE of wind power by 6%, offering 20-25% to grid parity thanks to its features, such as up-tower serviceability.
Minimize total life cycle cost & boost annual energy production
Annual energy production is a result of availability and efficiency. FusionDrive® is a reliable medium-speed solution. All high-speed components that are more prone to failure have been removed from the design and this leads to highest availability. PMG also enables greatest efficiency curves, and this makes a winning combination to boost annual energy production.
Unbelievably small size enables manageable transport and assembly and a shorter drive train. Scalable platform extends from 3 MW to offshore class – in onshore size. The integrated drivetrain’s size also simplifies the turbine's structural design and boasts lowest nacelle weight, improving total turbine cost competitiveness in the market.
High level of annual energy production and a minimum total life cycle cost is the formula for lowering the cost of energy!
Reliable medium speed technology – highest availability
The FusionDrive has no slip-rings and no rotor windings. It has low cogging torque and no bearing currents. Its medium speed bearings have no smearing risk. Total amount of bearings is low, as no high speed bearings or generator bearings are needed. A common lubricant oil space provides controlled environment for force transferring rolling components. Gear stages and generator are perfectly aligned. No extra bearing forces or induced vibration appear. FusionDrive also has efficient air cooling system inside the generator.
Best serviceability in the market
FusionDrive® requires minimal maintenance. Right from the beginning, FusionDrive® has been designed with easy serviceability in mind — FusionDrive can be completely maintained without an external crane. The gear and generator can be split, and all components are changeable in the nacelle. Small size, simplified turbine and great serviceability together bring down total lifecycle costs.
1. All main components can be disassembled and serviced up-tower.
2. Second planetary stage can be disassembled and serviced up-tower.
3. The generator can be disassembled and serviced up-tower.
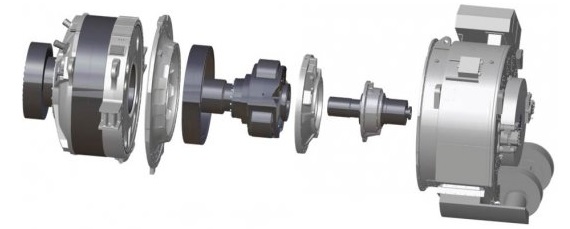
Technical specifications below are for FusionDrive 3 and 7. Please note that the product is scalable to any power class, up to 10 MW.
Weight and total length are dependent on rated generator output power.