Continental Conveyor
Heavy Duty Apron Feeder
Featured on Continental Apron Feeders
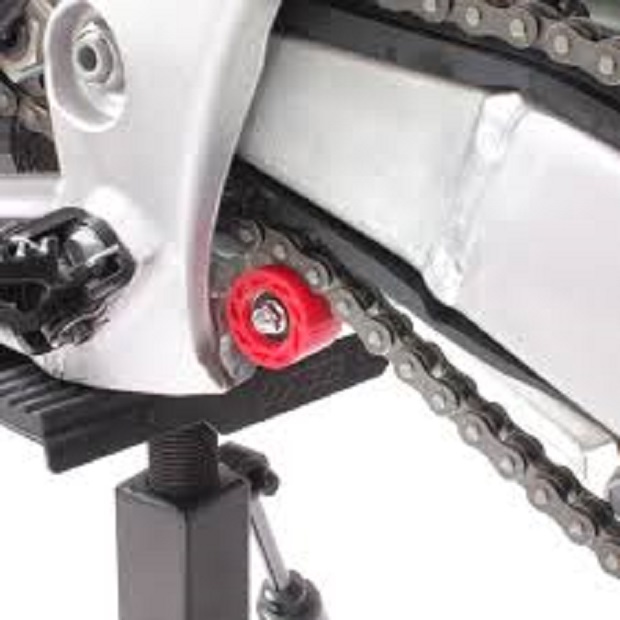
Chain and Rollers
The rugged design and popularity of crawler tractor chain makes it particularly well suited for the severe environment of the apron feeder application. The various available standard pitches and tensile strength ratings of this chain allow a suitable selection for all widths and lengths of apron feeder applications. Carrying and return rollers have hardened wheels and pins for long wear life. The large lubricant reservoir is factory sealed for life. Rollers have a single flange for positive tracking of the chain. Carrying and return runs use the same roller in order to minimize spare parts requirements.
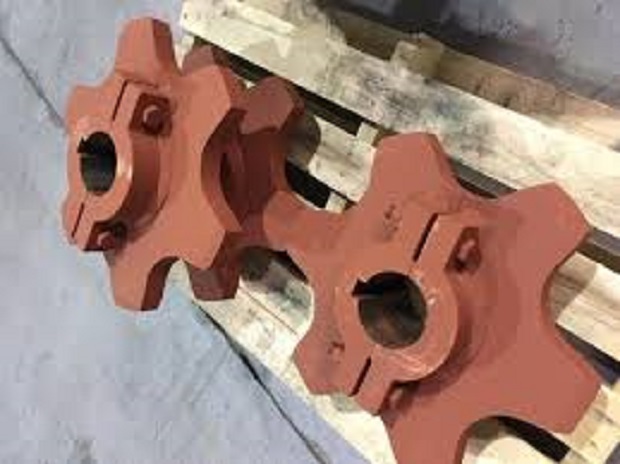
Sprockets and Traction Wheels
Sprockets and traction wheels with segmental rims are a standard feature on Continental heavy duty apron feeders. The segmental rims are machined and jig drilled to fit on the mounting hubs, which are keyed to the shafts. Sprocket segments are easily removed for replacement and can be reversible for double life. If possible they are “hunting tooth design“ to achieve full contact of all the teeth in two revolutions of the sprocket thereby promoting even loading and wearing of all teeth.
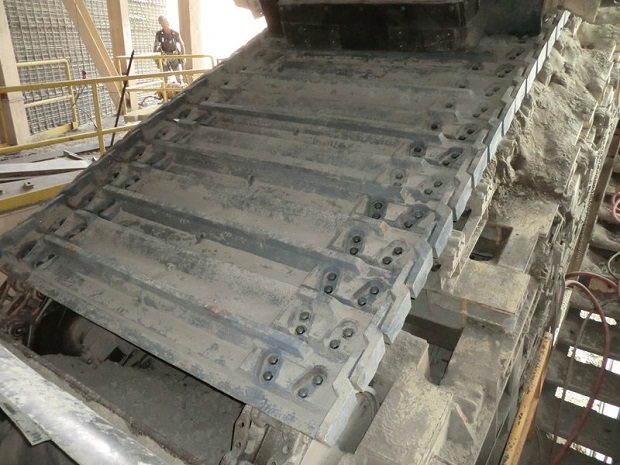
Cast Manganese or Fabricated Pans
Cast manganese is a work hardening steel alloy that is the best material for high impact or abrasive applications. Impact ribs cast into the pan longitudinally, combined with the impact rail on the feeder structure, reduce material leakage between the pans by limiting excessive deflection. Raised pads cast laterally into the pans provide a smooth mounting surface for the chain. For most average conveying and feeding applications where high impact and abrasion is not present, double beaded overlapping formed steel pans fabricated from mild steel or abrasion resistant plate are suitable. When combined with an impact rail to limit deflection, they are also suitable for applications with a moderate level of impact.
Continental Conveyor, established since 1963, specializes in the design, engineering and manufacture of mechanical bulk materials handling equipment and systems. Industries served include: cement, pulp and paper, mining, reconstituted wood products, smelting and reduction, quarrying, chemical, power plants, ports, and marine trans-shipping.
Production is rationalized between 2 modern plants located in Thetford Mines, Quebec and Napanee, Ontario.
Production facilities include 40,000 square feet in Thetford Mines and 26,000 square feet in Napanee. Each plant is well equipped with the necessary fabrication equipment such as plate shears, press brakes, plate bending rolls, pantographs, and numerous welding stations and positioners of a variety of types. Each plant has a machine shop that is able to perform most of the turning, milling and boring that is required for the equipment being manufactured. Both plants have their own indoor facilities for shot-blast cleaning and painting.
Our total staff includes: 80 plant employees, 16 mechanical designers using AutoCAD, 3 professional engineers (2 mechanical & 1 structural), 3 project managers, 10 sales and approximately 10 support and administrative staff. Of the design and project management staff, 6 have extensive experience in supervising the installation and starting-up/commissioning of all the types of equipment that we supply. Together they have a wide range of problem solving skills gained from projects in many different industries and locations.
Our product range includes:
- belt conveyors
- screw conveyors
- conveyor pulleys and idlers
- belt conveyor scrapers
- en-masse chain conveyors
- bucket elevators
- screw reclaimers
- stoker reclaimers
- vibrating feeders and conveyors
- conveyors and bin activators
- apron feeders
Source: http://continentalconveyor.ca/images/product_pdf/Heavy_Duty_Apron_Feeder.pdf
Magazine
No information