CD Industrial Group Inc.
The Ten Step Troubleshooting Process
A Shift in Thinking
What happens when equipment suddenly stops working? The pressure is on! Everyone is busy troubleshooting, right?
But what does effective troubleshooting look like? Effective troubleshooting is a calm, methodical process where a very careful diagnosis is made and verified before a component is changed or repaired. It is the opposite of a scattered approach where someone starts swapping parts as fast as possible.
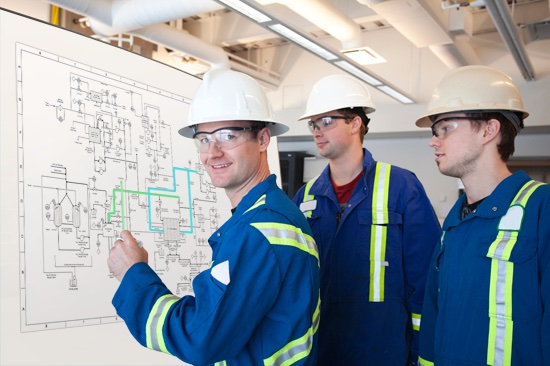
Effective troubleshooting is a repeatable process that can be taught and supported as a system and work process. It yields a long term solution instead of band-aid fixes.
What is the Ten Step Troubleshooting Process?
The Ten Step Troubleshooting Process (TSTP) is a carefully considered, thoroughly tested troubleshooting workflow created to help you solve system problems. It is a series of questions that will guide your thinking and help you quickly zero in on the root cause of the problem.
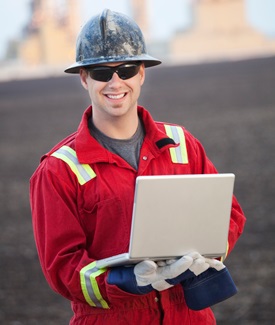
Why would I use the TSTP?
The TSTP has several advantages over conventional troubleshooting techniques.
- Having a logical plan avoids panic when the unexpected happens.
- Classifying the fault correctly at the beginning of the troubleshooting process means a higher time-on-tools ratio.
- Replacing only the needed and/or failed parts saves money.
- Doing preliminary work while the machine is running correctly saves time during troubleshooting.
- Clear, consistent & easy process allows one troubleshooter or the whole team to respond to problems.
- The TSTP allows the process to be logged and continued after a shift change in the repair shop.
- Equipment is completely repaired and returned to its optimal condition in the first shop visit.
Source: https://www.cdiginc.com/ten-step-troubleshooting-process
Magazine
No information