Flexible Lay Flat Ducting systems are ideal for positive pressure applications. Seams and grommets are welded to be airtight, providing low airflow resistance.
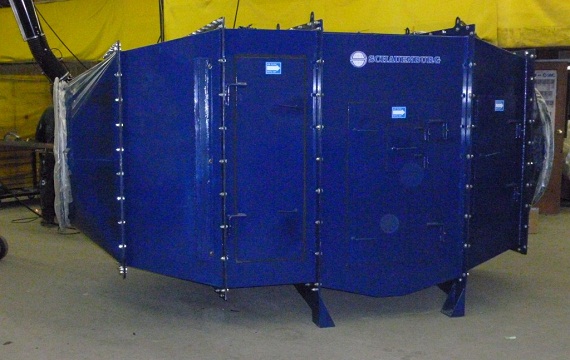
Principles of Operation
The cleaned air passes through to the main fan and rejoins the exhaust air circuit, or is discharged to the ambient atmosphere. By adjusting the flow rates and pressure of the intake water line, large variations of dust capacity and air flow rates can be accommodated.
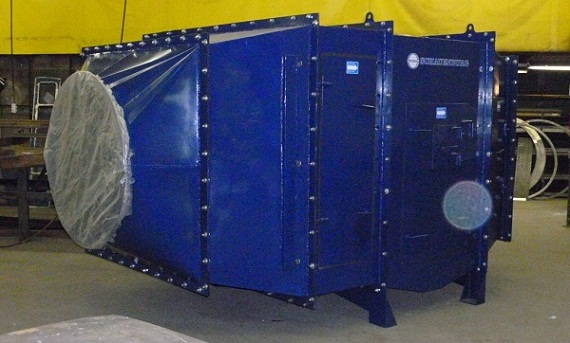
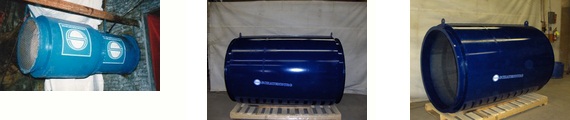
The Fan Silencers have been developed over the years by improving on a basic concept. With noise reduction, strength, long lasting and ease of maintenance as criteria, our design offers the optimum in fan noise suppression.

Manufactured to customer specifications, we offer a com-plete line of industrial tarpaulins, curtains, welding curtains, weather barriers, customer designed protective coverings, as well as, repairs on most PVC based tarpaulins from oth-er manufacturers. Customers can choose from different weights, materials, anti-static composition, UV protection, and fire retardant based on their specific application.
Phenolic Resin: The Manufacturing Difference That Results in a Better Product
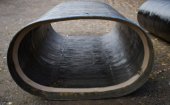
Destruction Test
• Greater stiffness allows higher negative pressure capability at equal weights.
Property | Schauenburg Phenolic Duct | Polyester Duct | Interpretation |
Impact Test (In-LBS) |
88 | 72 | Ability to resist a point impact |
Flex Strength (PSI) (Normalized) |
58,619 | 66,6676 | Load bearing strength |
Flex Modulus (KPSI) |
2325 | 1534 | Stiffness |
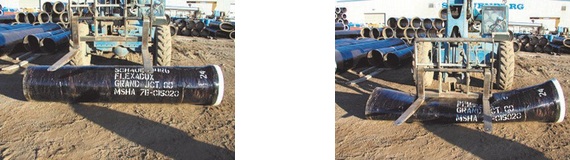
Destruction and Presure Test Video

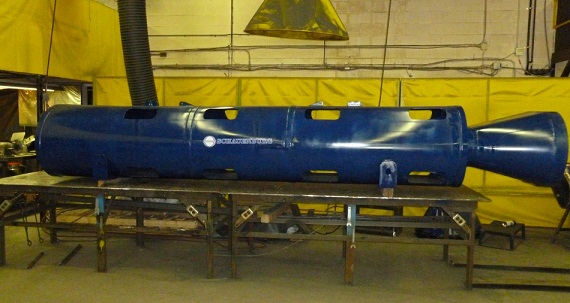
The Schauenburg Cassette System was originally designed to facilitate the installation of flexible ventilation ducting in rapidly excavated headings and consist of three basic components: the fan cone, the duct storage cassette and the draw off cone. The duct storage cassette normally holds 100 m of flexible ventilation ducting and consists of an outer casing and an inner tube, the annular space between the two pieces being the storage area for the ducting. A draw off cone is attached to the inner tube to facilitate orderly pay out of the ducting and smooth airflow through the cassette unit. The third portion, the fan cone, is used to direct the air from the pressure fan through the centre cone section and remain attached to the fan when removing and installing replacement cassettes.
Advantages
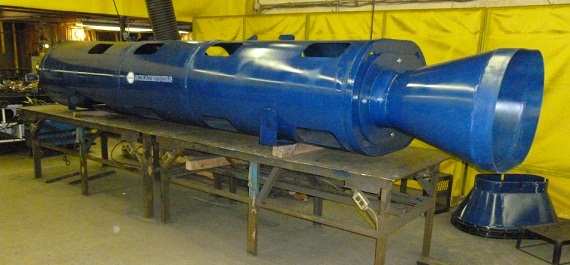
Schauenburg Industries Ltd. is a leading manufacturer of dog agility tunnels supplied to all of North America. Our tunnels are extremely durable, made from 14-16 oz/yd PVC fabric that is UV resistant to fading, weatherproof and mildew and rot resistant. All tunnels are 24" diameter and come in standard 10', 15' and 20' lengths. Special lengths manufactured as required. You have a choice of 4" or 6" coil pitch. Pitch refers to the spacing of the wire ribbing. We also manufacture Tunnel Saddle Bags complete with carrying handle straps. The Tunnel Saddle Bags are placed at the openings to secure the tunnel. The saddle bags will not compress the tunnel. The wide joining strap rests on the spirals of the tunnel. Tunnel Saddle Bags are available in all colours.