Pepper Maintenance Canada
Thickness Testing
Ultrasonic Testing (UT) uses high frequency sound energy to conduct examinations and make measurements. Ultrasonic inspection can be used for flaw detection/evaluation, dimensional measurements, material characterization, and more. A typical UT inspection system consists of several functional units, such as the pulser/reciever, transducer, and display devices. A pulser/receiver is an electronic device that can produce high voltage electrical pulses. Driven by the pulser, the transducer generates high frequency ultrasonic energy. The sound energy is introduced and propagates through the materials in the form of waves. When there is a discontinuity (such as a crack) in the wave path, part of the energy will be reflected back from the flaw surface. The reflected wave signal is transformed into an electrical signal by the transducer and is displayed on a screen.
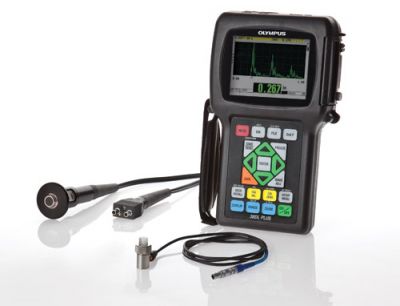
Typical Uses
Thickness testing is frequently used to monitor metal thickness or weld quality in industrial settings. Technicians equipped with portable UTM probes reach steel plating in sides, tanks, and piping. They can read its thickness by simply touching the steel with the measurement head (transducer). Contact is usually assured by first removing visible corrosion scale and then applying petroleum jelly or another couplant before pressing the probe against metal.
Advantages
• Non-destructive technique
• Does not require access to both sides of the sample
• Can be engineered to cope with coatings, linings, etc.
• Good accuracy (0.1 mm and less) can be achieved using standard timing techniques
• Can be easily deployed, does not require laboratory conditions
• It is sensitive to both surface and subsurface discontinuities.
• The depth of penetration for flaw detection or measurement is superior to other non-destructive testing methods.
• Electronic equipment provides instantaneous results.
• Detailed images can be produced with automated systems.
• It has other uses, such as thickness measurement, in addition to flaw detection.
Source: https://www.peppermaintenance.com/node/397