Armtec
How Our Mitchell Soundwalls Plant Drastically Improved Its Health & Safety Performance
It's been a positive year for Armtec Health & Safety as some of our operations are showing marked improvement in their Health & Safety performance. The latest to shine is the Soundwalls Manufacturing Plant in Mitchell, Ontario - their performance has improved significantly over the past few years and if you were to talk to anyone working there, you'd hear resounding pride.
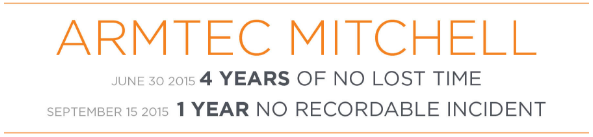
Mitchell Plant Manager, Dwight Rerup, says, “As of September 15, the plant has reached a new Health & Safety milestone of 1 year with no recordable incidents. We also surpassed the 4 year mark with no lost time injuries, as of June 30. It has been a continuing goal to reduce injuries and incidences to make the facility a safe place to work. Our team has taken a proactive approach to health & safety, rather than a reactive one, anticipating issues before they arise and putting in place measures to prevent accidents from happening.”
Production Coordinator, Richard Butson, points out that changing the attitudes and actions of everyone working in Mitchell has not been a quick or easy task. “By adopting a policy of providing employees with daily Safety Huddles and mandatory monthly Safety Talks, we have focused a great deal of attention on safety and over time the culture has changed to a point where the culture is enduring,” he says.
“I am extremely proud of the results that our plant has been able to achieve when it comes to Health & Safety,” reports Andrew Rush, the Vice President / General Manager of Armtec’s Soundwalls unit. “Working safely isn’t something that our team just talks about, they live and breathe it every day by ensuring that they, as individuals, are acting safely and that the people that they work with are also acting safely.”
Andrew continues, “Every new process that is implemented has health and safety considerations at the top of the agenda. This ownership level has been built up over time through the implementation of the various means; our national HSIP programs, Safety Huddles, a thorough implementation of Standard Work Procedures, inclusion in a Workplace Safety group with other companies, incorporation of on-site Health & Safety help into the role of the Production Coordinator, and the adoption of a rigour and discipline with regards to investigating incidents when they occur.”
Mark Anderson, President and CEO of Armtec, says, “It is rewarding to see one of our larger precast operations achieve 1 year without a recordable incident. The Soundwall employees, at the Mitchell plant in particular, demonstrate that a committed and engaged team can achieve great results. I am proud to have a precast operation reach this level and set such a positive example for the rest of the business!”
Mitchell’s best practice safety approach checklist
It’s certainly not a fluke that the plant’s Health & Safety performance is increasingly strong. While many initiatives are already required by law, leadership there has invested the time and money into some key extra programming and training for their employees. These include, but aren’t limited to:
- An expanded Production Coordinator role to include Health & Safety program development to provide hands-on direction at the plant level promoting the safety culture.
- An Employee Hazard Alert Program.
- An Employee Suggestion Program.
- Annual Safety Week (held each January) which focuses on aspects of working safely.
- An investment in outside certification training for higher risk activities and machinery (for example: crane, lift truck, wheel loader, shunt truck and aerial lift platform).
- Membership and participation in WSIB Safety Groups.
- Membership and participation in the local WSPS Network, Knowledge and Exchange Group.
- Supervisory competence education in the form of the WSPS Supervisory Responsibilities and Due Diligence course.
- Power Tool safety training.
- The design and implementation of SWPs (work instructions for every job which include safe work practices).
- An acquisition of an MSDS Management System, and partnership with CCOHS (Canadian Center of Occupational Health and Safety).
- An investment in first aid and AED training for all supervisors, lead hands and JHSC committee members.
- A collection of up-to-date, accessible and well-maintained training matrices to ensure compliance to meet both internal and legislative requirements.
Rolling 12 month TIR & Incident Rate
The chart below show’s Mitchell’s impressive drop in injury frequency since 2013, spending some time below company targets in 2014.

An attitude, a responsibility and our commitment
Andrew Rush offers, “At our locations, we continually encourage all employees to understand their respective rights and empower them to speak up if and when unsafe conditions are witnessed. Most importantly, we keep the lines of communication open for all employees and allow feedback – this creates positive engagement and a desire to stay involved.”
"Everyday we’re practising Health & Safety at Mitchell. We do daily huddles in the morning which I think are a great thing, it’s where we talk about any near-misses or issues that we have. Things have changed dramatically over the years… it’s really preached ‘safety first’ before anything else – so everyone goes home to their family at the end of the day."- Bill
"I feel the Health & Safety here is really good, I’ve seen the improvements of everything – getting better and better every year. I feel really safe myself… We have a lot of guidelines we follow, so even for new people, we watch over them to keep them safe as well."- Dan
"We have made the Shipping Department one of the safest places to work in in Armtec Mitchell. We work together as a team to ensure we work safe and look out for each other. We recognize hazards before they happen."- Bob
"We’re very proud of our performance… If there’s something [a worker] doesn’t trust, they will question it right away. They’re not afraid to refuse work if need be. We do our Safety huddles in the morning and I think that makes a big difference, everyone is thinking safety first thing – we wake them up with safety! …If someone needs to report an immediate issue, we have our Hazard Reporting form, but as the Foreman I also instil into them that I need to know right away, that I need to fix the issue right away."- Mike
"In the past four years of working for Armtec the attitude towards safety has only gotten stronger. With the safety huddles and yearly training days it keeps your Health & Safety at the front of your mind. Every day and every new job become an opportunity to practice what we learn so that at the end of the day we can all go home whole, and most importantly, alive."- Sarah
"As an employee here for many years I like the Health & Safety atmosphere here and it is always evolving to meet the needs of new jobs and a new workforce. All issues are dealt with quickly, big or small, and communicated well both at Daily Huddles or Townhall Meetings."- Clint
Source: https://www.armtec.com/news-article/mitchell-health-and-safety-records/
Magazine
No information