Spectrum Technologies Ltd
Paper Analysis
Uniformity is Key to Efficient Operation
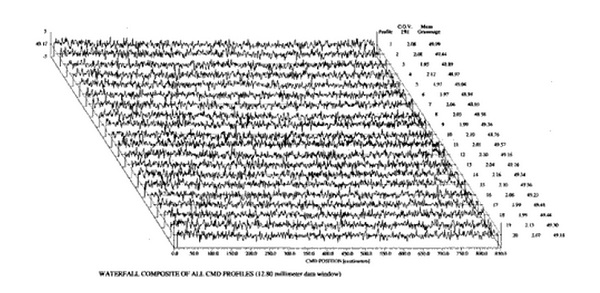
The uniformity of paper is of fundamental importance to the final product. Of the different types of uniformity, the basis weight and caliper uniformity are the most important. Without this uniformity a host of problems arise, including wrinkles, breaks, and misregister in the pressroom. Due to the importance of these properties, continuous on-line scanners have been developed to measure them.
On-line scanners have a number of limitations. Since the paper travels through the scanner in the machine direction while the scanner moves across the machine, the scanner is really measuring the paper in a triangular fashion. The algorithms in the scanner then determine the MD & CD components, to the best of their ability. Another limitation of the scanner is the low frequency response inherent in the radioactive (Beta) source. Different scanners filter the signal differently, and use different algorithms for separating the MD from CD. Thus to compare the values from one machine to the next is imprecise.
To measure your paper without the limitations of the on-line scanners, it is recommended that the basis weight and caliper of your paper be tested in both the MD & CD on an off-line profilograph, or TAPIO. The TAPIO unit is the closest instrument to a standard at the present time. Because of this, a benchmark of your paper uniformity compared to other machines can be obtained.
The CD strips, collected from the top of the reel, represent a true cross-direction profile. There is no possibility that MD components will confuse the analysis. A machine direction component is also obtained, due to the spacing between the strips. Finally a residual component that cannot be related to the MD and CD is determined. This component is used to determine headbox performance and is used by manufacturers to warranty the headbox.
To overcome the low frequency response of the Beta gauge in the mill sensor, MD butt rolls are slit from the parent reel on the winder. When these rolls are measured in the off-line scanner at low speed, the frequency response normalized to paper machine speed is very good. This gives a frequency response reading greater than 200 Hz, much higher than on-line scanners.
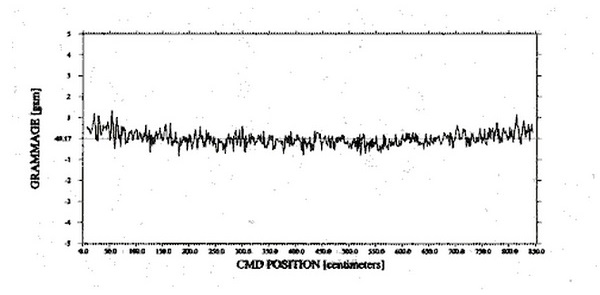
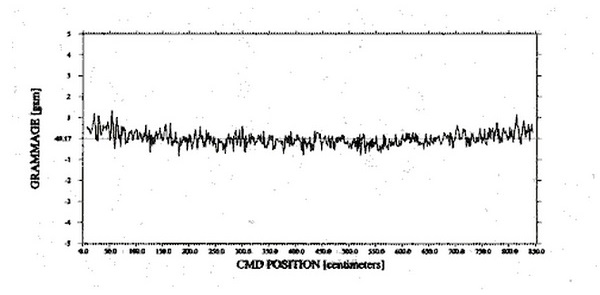
If there are basis weight variations, the source can be inaccurate transducers, problems with screens or pumps, or inadequate mixing in upstream chests. A wet end survey is recommended if there are excessive basis weight variations.
A paper analysis is recommended on an annual basis. If, however, there is any suspicion of a problem, or after any major equipment change or machine speed-up, a paper analysis is also recommended.
Source: http://www.spectrum-tec.com/english/pulpandpaper/paperanalysis.html
Magazine
No information