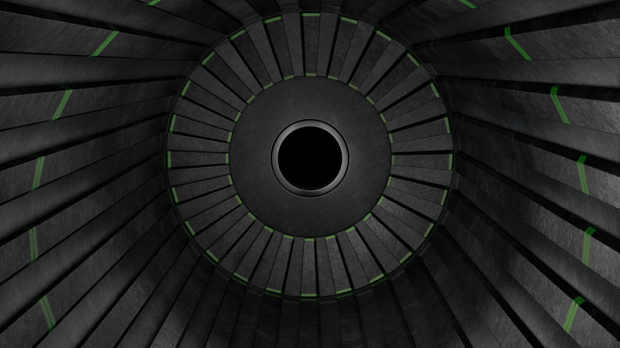
How can minerals processors get the most value from a mill liner supplier?
Grinding mill liners are critical – they provide the shell and heads with protection from impact and abrasion wear, and transfer power to the charge to create the tumbling (or cateracting) motion necessary to grind the ore.
Relining of a mill is the single largest aspect affecting mill availability for production and is a time consuming, necessary maintenance event, which makes the selection of a mill lining supplier one of the most important choices in the entire operation.
When choosing a mill liner, most mill maintenance engineers and production managers focus almost exclusively on its price and wear life.
However, the supplier’s ability to ensure good fit of the new lining, and appropriate geometrical design that will deliver the best mill process performance are also important considerations to ensure mill availability, throughput and product quality.
Transitioning from OEM liners
Minerals processors usually purchase the first set or two of mill liners from the mill original equipment supplier because it’s a requirement for the mill supplier to provide the start-up lining to uphold throughput performance warranties.
These first liners are usually conservatively designed to lower the risk of liner damage during commissioning and early operation, when disruptions in feed to the mill and electrical trips are common.
However, once stable mill operation has been achieved it regularly becomes necessary to revise the mill liner design to optimise mill performance and adjust to changes in ore characteristics over the life of the plant’s operation.
During this revision process, it is beneficial to look at alternative suppliers, to ensure you’re getting the most value for your operation. Here’re a few capabilities that you should be looking for in your search.
What are your liner’s wear life requirements?
Longer liner wear life can increase the mill’s availability or its volumetric capacity.
The best wear life for a liner isn’t always the longest – it’s important to consider how your liner life will fit into the overall plant’s maintenance planning and campaigns.
This is crucial for preventing each piece of machinery being stopped independently for maintenance, and ideal scheduling coordinates timetables to keep production stoppages to a minimum. This means that your required mill lining wear life is based on your most efficient shutdown schedule and needs to be reviewed often.
Once the desired mill lining wear life is identified, trials should be conducted to determine the wear life of competing suppliers and how they match maintenance schedule requirements.
To fairly compare wear life between suppliers a direct comparison trial is necessary - involving components of identical geometry from prospective suppliers installed in the same zone of the mill and put through side-by-side production tests. Periodic wear rate measurements demonstrate the performance of competing materials.
A longer-wearing product may provide opportunity to extend the mill operation between relining campaigns or may allow the lining design’s thickness to be reduced, increasing mill volumetric capacity.
Optimising liner geometry and energy use
Optimised liner geometry and grate flows provides improved mill throughput and grind quality, while effective charge motion reduces energy and grinding media consumption.
Look for suppliers who can demonstrate mill process knowledge and experience in optimising liner designs to improve throughput, product grind quality and energy efficiency.
These companies usually have many years of experience in supplying mill liners and have highly experienced product and service engineers capable of consulting on wear patterns, with a deep understanding of how liner geometry influences mill charge dynamics.
However, the best suppliers combine proven experience with a willingness to innovate their designs using the capabilities of modern advanced mill simulation tools.
Two- and three-dimensional simulations analysing charge motion and impact energy can be used to identify and resolve potential for packing between lifters, while wear analysis software provides data to optimise the geometry of new or existing liner systems, supporting performance life warranties.
Effective charge motion delivers monetary benefits including lower energy and consumables consumption, improved downstream recovery and prevents excessive abrasion cause by charge sliding.
Modern suppliers should also be using computational fluid dynamics (CFD) and single particle hydrodynamic (SPH) modelling software to analyse pulp flow in mills fitted with grate discharges, ensuring that the evacuation of pulp from the mill is optimal, avoid slurry pooling and slurry “short-circuiting” which reduces mill throughput and efficient power consumption.
Designing a replacement liner for cost-effective maintenance
Mechanical design skills should be at the top of your list when selecting a new supplier, as they will often have to measure the mill internally to determine accurately how to dimension the liner components for a good fit.
Although shell internal dimension and liner bolt drilling drawings may be available it is always wise to verify these details through site measurement, preferably using 3D scanning technology in case deformation or wear have altered its dimensions.
Fitting problems in relining can easily extend shutdowns, leading to significant production losses.
Innovatively designed liner sets with fewer components and safe handling features can reduce relining time, however these require a supplier with robust manufacturing capabilities and service engineers who’ve spent time familiarising themselves with your site’s maintenance practices and safety concerns.
Summary
To fully realise the value of your mill liner, you need to consider all aspects of its design and purpose.
Choosing a supplier that has the appropriate competencies, including mechanical design, modern simulation tools, advanced materials technology and a deep understanding of your process requirements is key to maximising your mill’s availability, efficiency and performance while decreasing maintenance.
The true value of mill lining needs to be measured in total ownership cost and return on investment, in how a supplier can provide a lining which supports your maintenance schedule, reduces stoppages and ultimately lowers per ton production costs.