Spectrum Technologies Ltd
Oxbow Effect
Caliper Uniformity at the Edge of the Reel
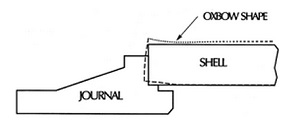
This growth at the ends is known as the oxbow effect. This results in over-calendering the edges, soft edges, and cracks in the paper on the reel.
To counteract this tendency, the ends of calender rolls are insulated. With well-designed insulation the calender will run with no problems at its design temperature and trim. If the ends have too much insulation in them, the roll will be too cool at the ends with too small a diameter. This results in high caliper paper at the edges or hard edges on the reel. This reel build problem can again cause breaks in the paper edge.
The solution is to ensure that the calender rolls have the correct amount of insulation to minimize the distortion. To accurately determine the amount of insulation required, an accurate model of the calender roll must be created. This requires the knowledge of its temperature profile and boundary conditions. Typically the temperature profile of the calender roll is measured along with the sheet temperature, water temperature and air temperature. This temperature profile, along with the calender stack speed is used to calculate accurate temperatures throughout the calender roll and the thermal distortion of the calender roll. Different configurations of insulation can then be modeled to determine the effect on the distortion profile. The insulation configuration that yields minimal distortion is the one selected for use.
Source: http://www.spectrum-tec.com/english/pulpandpaper/calenderoxbow.html
Magazine
No information