Wolseley Canada Inc
Case Studies
Reducing injuries in Canada
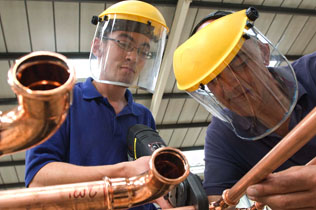
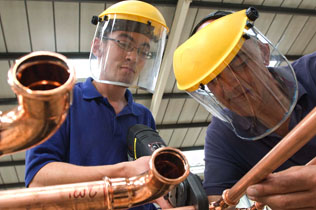
By July 2012, Wolseley Canada had reduced work-related injuries by over 40 per cent and lost workdays by over 67 per cent as a result of the ongoing implementation of the Occupational Health and Safety Management System (OHSMS) 18001. The process involved a detailed gap analysis, new policy development, best-practice sharing initiatives, job hazard analysis and a commitment to ownership by branch management. A bi-annual health and safety Facility Self-Assessment was initiated in 2011/2012 to continuously self-evaluate branch safety performance. A financial reward is given to those branches that achieve 90 per cent conformance to the OHSMS 18001 Assessment. To date, over 80 per cent of the branches in the programme have a score of 90 per cent or better.
Strengthened central support for health and safety - Nordic region
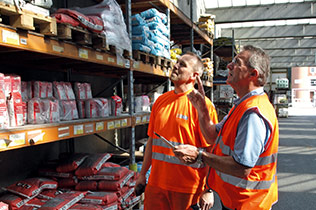
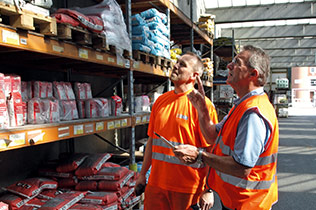
The Nordic region has enhanced its central health and safety team, which now consists of seven business partners working throughout Denmark, Sweden, Norway and Finland.
Their job is to support local health and safety initiatives and to perform audits to test branch compliance with national legislation and Group minimum requirements. To support this initiative the business has implemented a new IT system. Each business partner uses a mobile tablet to complete checklists on-site.
The result of each audit is automatically sent to the relevant Branch Manager as an action plan, with relevant photo documentation attached. The Branch Manager is required to complete all recommended actions before the agreed deadline. A copy of the report is sent to the local health and safety employee representative and the regional manager. The system provides management with useful real-time information on health and safety for each site.
Ferguson focus on customer service
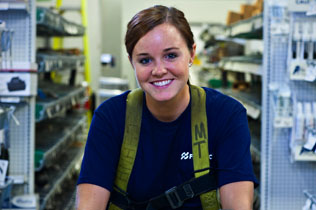
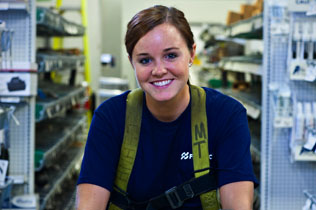
This year some of Ferguson's well-established customer service training programmes were targeted to specific high-impact roles, such as counter sales associates. The counter training programme focuses on several areas including the inventory mix, stock levels, merchandise displays, the floor plan and layout, building customer relationships, and sales training. Feedback and findings from the secret shopper programme were integrated into the training and used as a teaching tool, to recognise outstanding behaviour and to identify opportunities for improvement.
Lean management at Wolseley France
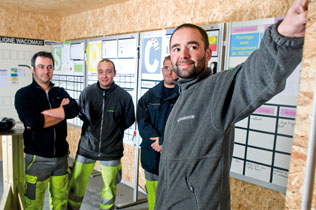
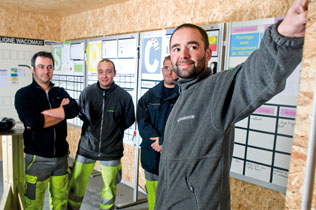
The import and wood solutions business in France has recently implemented Lean Management practices. Groups of between 12 and 20 employees, led by a team manager, work together to complete required tasks and take individual responsibility for areas such as health and safety or quality management. Team managers are appointed through an assessment process and team workers receive training, coaching and support to transition to the Lean Management approach. This method has improved productivity and has engaged and empowered employees in the running of the business.
Ferguson sales training
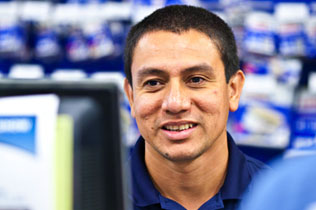
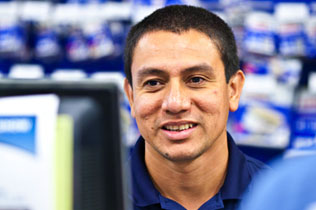
Ferguson sales employees routinely engage in product knowledge training and sales methodology training. Using a role-based curriculum, targeted high impact training programmes are delivered. These programmes are designed to improve performance and change behaviours. All programmes are based on a blended learning strategy comprising classroom training, on-the-job coaching and self paced learning. The training curriculum includes business planning, customer account planning, leadership development and process training. Each month on the Ferguson intranet home page, a specific sales training offering is presented in the No Train, No Gain spotlight. This web-based FastTrain module targets a specific element of profitability training. Topics touch on concepts such as selling value vs. price, closing the sale or dealing with customer objections.
Third year of partnership with Impetus Trust
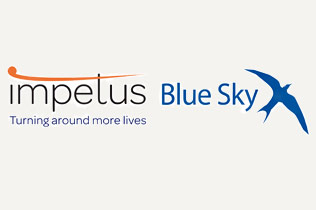
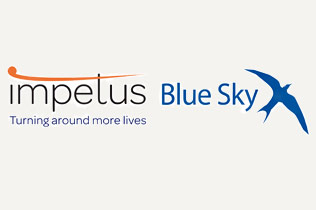
Impetus works to break the cycle of poverty by investing in ambitious charities and social enterprises that fight economic disadvantage through helping people to gain education, skills and jobs. It uses a highly effective venture philanthropy model, consisting of management support from the Impetus investment team, pro bono specialist expertise and strategic funding, to accelerate the growth of those organisations. This has led to impressive growth rates in charities Impetus has supported, on average increasing their annual income by 31 to 40 per cent. Included in the Impetus portfolio is Blue Sky Development and Regeneration.
Blue Sky is a charity which gives paid work to people coming out of prison, to enable them to move successfully into long-term employment. As part of its scale-up plan, which Impetus and Wolseley are backing, this social business has significantly increased the number of employment contracts offered to ex-offenders, hiring more than 650 to date - enough to close a small prison.
"60 days of caring" - USA
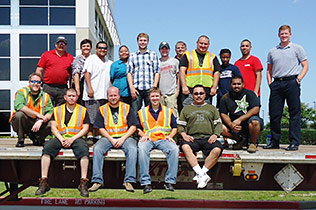
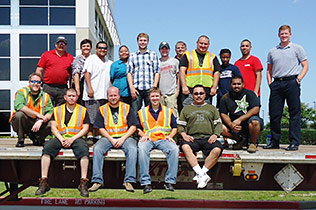
In honour of the US business’ 60 year anniversary, employees in more than 225 Ferguson locations, including the company’s headquarters in Newport News, Virginia, participated in a nationwide “60 Days of Caring” campaign to give back to and strengthen the communities where they live and do business. Employees and partners donated approximately 20,000 lbs of food to 101 charitable organisations throughout the United States, including animal shelters, food banks and youth development programmes.

Stark, a business unit in the Nordic region, is acting as a sustainable leader, being the first construction distribution business in the country to invest in forklifts with fuel cells that run exclusively on hydrogen.
Hydrogen powered forklifts - Nordic region

Stark, a business unit in the Nordic region, is acting as a sustainable leader, being the first construction distribution business in the country to invest in forklifts with fuel cells that run exclusively on hydrogen.
Since November, trucks in operation at the Stark City store in the Copenhagen area all use fuel cell technology. The forklifts create zero pollution, the only “waste” being completely pure water – which is discharged by the heating fuel cells as steam.
Additionally, the trucks only consume hydrogen when they are being driven or are lifting. When the truck is stationary, for example when handling items, no energy is consumed – unlike diesel forklifts that consume fuel even when idle. In addition to the trucks, the site also has its own hydrogen station which makes refuelling quick and easy – it takes only three to four minutes to refuel a tank
Lean and green - USA
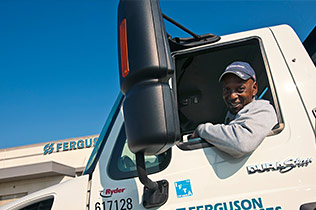
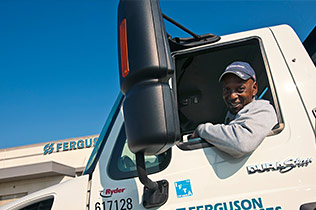
The US business recognises that moving towards more environmentally sustainable business practices makes good sense. Significant efforts have been made to reduce the volume of waste sent to landfill, by improving the collection of recyclable waste, and by using plastic containers and pallets. Every distribution centre (“DC”) in the US business has its own baler, making it possible to compact its own cardboard and plastic. The DCs also backhaul cardboard and plastic from the branch network. This recyclable waste is then sold for the manufacture of items such as paper, new boxes and packing materials. As well as meeting its environmental objectives, the business also saves money, especially on waste disposal fees. The DCs have almost eliminated the need for cardboard pallet-sized boxes to ship smaller materials to the branches by investing in re-usable plastic shipping totes and plastic pallets.
Consolidating I.T. data centres, cutting carbon
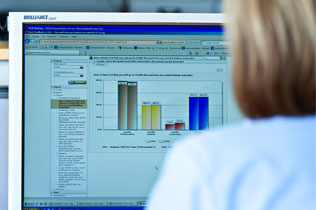
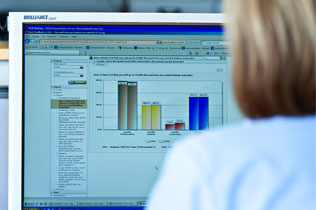
A project is underway across Wolseley Group to consolidate I.T. data centres and adopt 'virtualisation' technologies. The project is forecast to save circa 7.4m kWh of electricity per annum, through a combination of reducing the total number of servers and adopting newer technologies which draw less power.
UK headquarters achieves zero waste to landfill
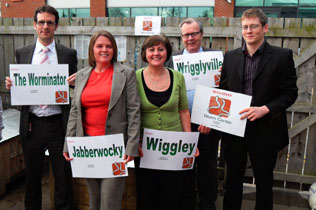
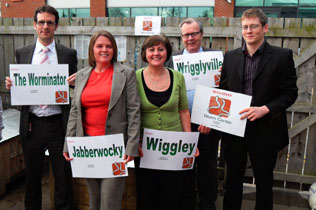
Wolseley UK's Leamington Spa site, comprising the Wolseley Center, the National Distribution Center (NDC) and the Sustainable Building Center now sends zero waste to direct landfill, after the three buildings all reached industry-leading waste targets. Following a complete change in the way waste is handled, 99.8 per cent of waste at the NDC and 97.5 per cent of waste from the Wolseley Center is now recyclable, meaning that just 2.7 per cent of the site's entire waste is compacted and sent for incineration to generate electricity. As part of the holistic waste management programme, wormeries were installed on site for the composting of food waste. The photograph shows Wolseley employees from the Leamington Spa office who won a competition to name the wormeries.
UK business awarded New Employer of the Year
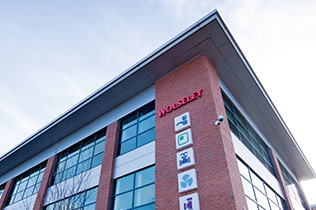
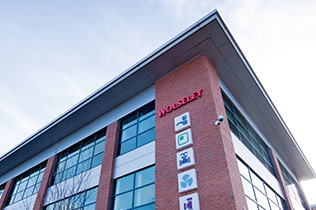
The UK business has been presented with the New Employer of the Year award by the National Mentoring Consortium (“NMC”), following its involvement in their Ethnic Minority Undergraduate Scheme.
The NMC works with over 300 employers and 15 universities to promote equality and diversity in graduate recruitment and to enhance the employability of black, Asian and ethnic minority students, particularly those with a disability or dyslexia. The programme provides support and experience to students seeking managerial and professional careers. The UK business placed four managers into one-to-one mentoring partnerships which helps prepare the students for working in a professional environment.
"Go Green, Stay Green" at Wolseley UK
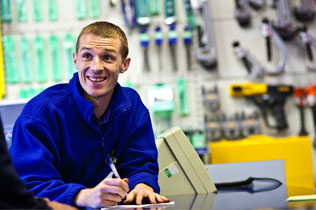
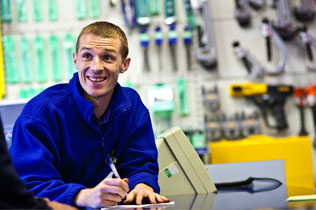
"Go Green, Stay Green" is a health and safety compliance tool that requires branch managers to assess their own performance against a number of criteria. The assessments are verified by independent branch audits and branches are supported in making any necessary improvements. The level of compliance with health and safety standards has increased significantly since the introduction of this programme. Management teams are engaged at all levels, including area sales managers, regional sales directors and brand directors, ensuring that the initiative and the results are owned by the business and that the profile of safety and compliance is raised.
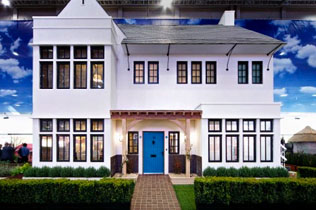
The Prince's Foundation for Building Community focuses on the impact that community building can have on people's lives. Since 2012 Wolseley has enhanced its support by joining the Corporate Partnerships Programme.
Enhanced support for the Prince's Foundation
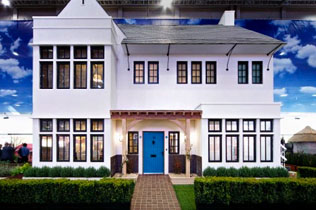
The Prince's Foundation for Building Community focuses on the impact that community building can have on people's lives. Since 2012 Wolseley has enhanced its support by joining the Corporate Partnerships Programme.
The Prince's Foundation's Corporate Partnership Programme forms long term partnerships with companies who want to engage communities and create practical solutions that help people live their lives more sustainably. Through partnerships we can positively impact communities through the products people buy, the quality of the buildings in which they live and the green spaces in which they come together.
The photograph shows The Prince's Arts and Crafts House, designed by the Prince's Foundation for the 2012 Ideal Home Show, and built in collaboration with corporate partners to show over 250,000 visitors how sustainable living can be stylish, comfortable and affordable, and benefit local communities.
Canada engage employees in managing health and safety
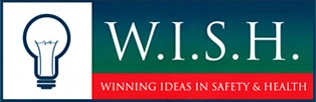
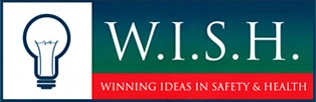
The W.I.S.H. contest (Winning Ideas in Health and Safety), originally implemented at Ferguson, was launched at Wolseley Canada. W.I.S.H. is a simple program that encourages the sharing of safety ideas, programs and best practices throughout the company. The health and safety management team solicited ideas from employees to improve safety in their locations, giving prizes to those whose ideas were taken forward. Winning ideas included the initiation of a "Defensive Driving Course" to improve driver skills and reduce collisions, a "Century Club" to award branches for every 100 days that pass free of lost-time injuries, a new parking policy, "Look in front, not behind", requiring employees to reverse into parking spaces, and "Safety information posting locations" in branches, making the latest information available in a number of locations including lunch rooms, wash rooms and battery charging stations.
Wasco introduces e-commerce site
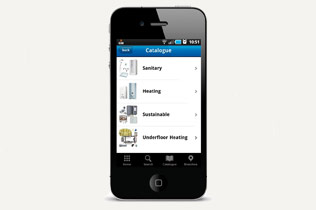
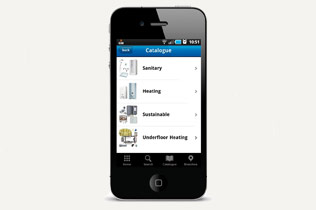
In April 2010, Wasco, Wolseley's plumbing and heating business in the Netherlands, introduced an e-commerce website, www.wasco.nl.
Customers can browse the site and also see suggested alternative or complementary products so that they can find exactly what they need.
The site complements Wasco's existing business, with online sales increasing by 25 per cent in 2010/11. Wasco is also launching a new version of Wasco mobile – a website and app which will include a bar code scanning facility.
Stark targets a new market
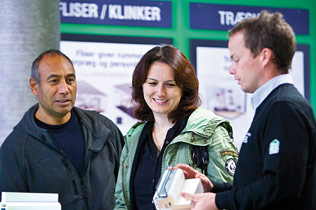
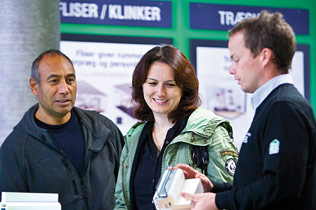
Stark, Wolseley's Danish building materials business, identified an opportunity to use its excellent knowledge and position as leader in the professional market to help private house owners with their building projects.
Stark now offers private house owners the same service and product advice as their professional customers.
More than 200 Stark employees have received training so that they can better understand the needs of private customers. Branches now have a dedicated green area for self build customers, containing product displays, marketing and product literature. These customers can also join a special members club, with benefits including offers and discounts, home visits and access to project advice and pricing. Since the concept was introduced in 2010, more than 71,000 people have joined.
Source: http://www.wolseley.com/index.asp?pageid=153