John Crane Canada
Equipment Service
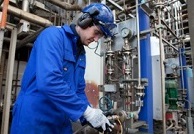
To reduce unplanned maintenance and avoid unnecessary replacement costs, John Crane Equipment Service oversees critical systems checks and plant equipment maintenance, as well as engineered component repair, removal and reinstallation services. Assistance can be provided during unplanned shutdowns to get equipment back up and running quickly, or during planned maintenance to optimize your process and achieve your shutdown window.
Risks of Misalignment
Due to the excessive vibration it can cause, inaccurate shaft alignment is one of the most common culprits of seal damage, bearing failure and coupling failure. Even the most conservative surveys indicate that 50 percent of all machine breakdowns are directly due to poor alignment, and some show that up to 90 percent of machines are running beyond their recommended tolerances.
John Crane understands the importance of proper alignment, and our engineers have a full set of diagnostic tools at their disposal to identify signs of misalignment or improper installation:
• Laser alignment
• Differential temperature measurement
• “As-fitted” applications data bank
Improving Reliability
All John Crane plant equipment maintenance services are available on a contract or as-needed basis. By scheduling timed, frequent health care checks, clients can uncover potential problems early on, providing opportunities for corrective or preventative measures that could help maximize uptime and limit the need for reactive maintenance. To identify possible risks, we evaluate the entire process — rather than just an isolated system — and then help optimize it to reduce maintenance costs and improve overall reliability.
We’re constantly expanding our number of global service centers to better serve the plant equipment maintenance needs of our clients. Find the nearest John Crane service center here. Looking for an even higher level of service? Consider our Reliability Support service.
Source: http://www.johncrane.com/Services/Equipment-Service.aspx
![]() |
Machine Shop Supervisor (Stoney Creek, Canada)
The Machine Shop Supervisor is responsible for leading employees in a manner to meet or exceed Company established KPI’s and targets for production, maximum quality, minimum scrap and the administration and enforcement of Company rules, policies and procedures.
Jr. Applications Engineer
Working within the John Crane Canada Engineering Services team, the Jr Application Engineer will directly support Drafting and Designing office and Aftermarket Technical Sales Teams by providing sound engineering analysis and review, responding to customer inquiries, and engaging with other members of John Crane's highly respected global engineering resources.
Customer Service Representative III, Stoney Creek Canada
The Customer Service Representative III assists John Crane Canada customers with all aspects of purchases and repairs of Mechanical Seals.