Outotec (USA) Inc
A Heritage R&D Project Produces a Breakthrough
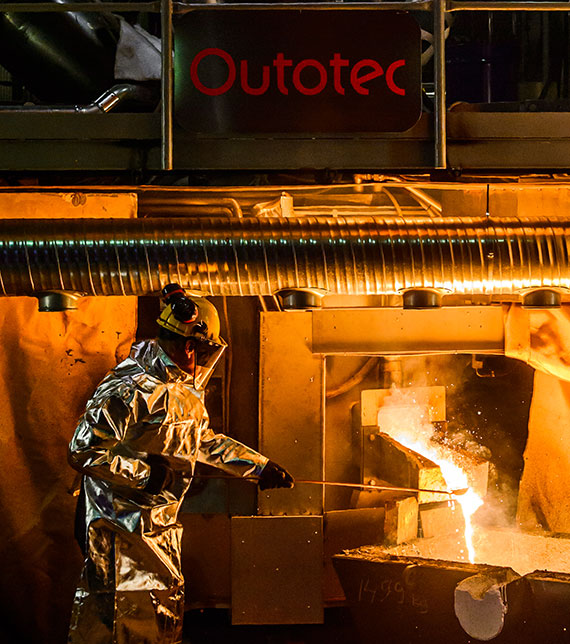
Outotec direct current (DC) smelting is a cost-efficient, small-footprint, and environmentally sustainable solution for ferroalloy processing. Suitable for a wide range of applications, it can be used for direct smelting of fine ores with no pretreatment and also offers a cost-efficient method for recycling challenging by-products such as dust from steel production. The capabilities and competencies of the Outotec Research Center have played a critical role in continuously developing and improving this technology.
DC furnace at the Pori Research CenterOutotec’s history with DC smelting stretches back to the 1980s, when it was first researched by Outokumpu. The process was revisited in 2011 when it was decided that the required technology was sufficiently advanced to make the process commercially viable, and construction of a pilot-scale DC furnace at the Outotec Research Center in Pori, Finland began.
“Developing our handprint by offering customers new sustainable technologies and services is a key driver of our R&D process, and DC smelting is a perfect example of this,” says Lauri Närhi, Outotec’s Technology Director, Ferroalloys Technology.
Typical applications include ferrochrome, ferronickel, ilmenite, and dust recycling in steel production, especially stainless steel. Highly flexible, DC smelting can be used for processing feed ores with very fine particle sizes, or those with highly variable chemical or mineralogical compositions. This flexibility opens up opportunities for making sustainable use of reserves that would not previously have been considered viable using conven- tional smelting technology.
In DC smelting, the feed material is gravity-fed into the furnace, together with the reductant, via charging tubes. A continuous direct electrical current is supplied by a transformer and rectifier, with a central graphite electrode forming the negative cathode and the bottom of the furnace the positive anode. The smelting energy is supplied by an open plasma arc, which can be likened to a giant welding torch. The alloy sinks to bottom and the slag floats at the top, while the off-gas produced is extracted and cleaned. The gas can be used as a combustible fuel elsewhere in the plant, helping to improve energy efficiency.
Cutting emissions
As regulations governing carbon emissions become ever stricter and the price of high-grade reductants such as coke continues to rise, producers are increasingly searching for more sustainable and economically viable alternatives. “DC smelting offers a significant advantage over traditional methods in this regard,” says Närhi. “As well as cheaper, lower-grade reduct- ants such as anthracite or coal, it can also make use of carbon-neutral bioreductants produced from renewable sources like agricultural waste. Using these types of bioreductants can help producers to reduce the carbon footprint of their operations and reduce their reliance on increasingly scarce fossil- fuel resources.”
Improving existing operations
One of the biggest potential sustainability benefits of DC smelting technology lies in recycling. It can be used to process and recover value from fine materials such as the dust that results from the production of steel and other metals. A steel plant can produce tens of thousands of tons of fine dust every year, and this material is very difficult to treat, often ending up in landfill sites.
Complementing existing smelting operations with a DC furnace significantly reduces waste volumes by enabling these fine materials to be recycled with no need for complex and expensive agglomeration or pelletizing equipment. Furthermore, the dust resulting from steel production, for example, contains valuable materials such as iron and zinc, which can be extracted using the DC process. For smaller-scale operations, Outotec DC smelting is a viable alternative to traditional smelting – the simpler layout and smaller furnace mean that the plant footprint is significantly smaller.
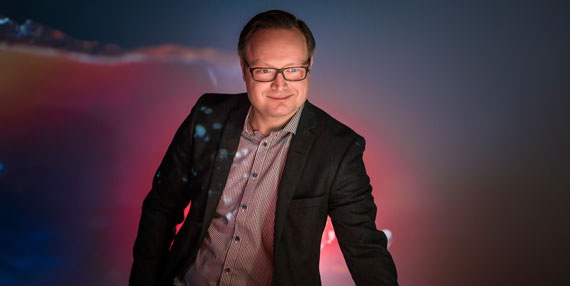
In the future it is hoped that the technology will play an im- portant role in supporting zero-waste production. “Zero waste is becoming an increasingly important goal, particularly in Europe,” Närhi points out. “This is where 100 percent of the materials entering the plant either leave as finished product or end up being reused, recycled, or converted into energy – with none going to landfill. The ability to recycle and recover valuable met- als from previously dumped material offers huge environmental and economic benefits for producers.”
Maximixing our handprint
• Reserves not viable using conventional smelting can be processed, reducing waste
• Off-gas produced can be used elsewhere in the plant, improving energy efficiency
• Can employ carbon-neutral bioreductants to help producers reduce their carbon footprint
• Brings customers closer to lean zero-waste production
Source: http://www.outotec.com/en/Sustainability/Cases/A-heritage-RD-project-produces-a-breakthrough/
![]() |
Field Service Representative
To provide field advisory services for customers on existing and/or newly acquired equipment and components.
Operational Purchaser
As Operational Purchaser you will be responsible for assigned purchase order processing and inbound process monitoring related tasks in the Customer Logistics organization for North & Central America.
Field Service Technician
We are now looking for one Field Service Engineer for Automation/Analysers to join the Service team in Canada.
The position is based in Canada to support customers across the country.