Outotec (USA) Inc
Flotation's Sustainable Future
Declining ore grade quality and increasing pressure to improve the energy efficiency of operations has led to significant advances in flotation technology in recent years. As the global market leader in flotation, Outotec focuses its R&D activities on developing sustainable solutions that help producers reduce their power consumption and carbon footprint while ensuring the long-term economic viability of their operations.
Although flotation technology has been around for over a century, today it is advancing more rapidly than ever, largely due to the physical capacity and energy efficiency of flotation cells.
In basic terms, flotation involves mixing ground ore with water to form slurry, which is then fed into flotation cells that are aerated to produce bubbles. The particles in the slurry attach themselves to the air bubbles, which rise to the surface, forming froth, which is then removed from the cell as concentrate. The heart of the cell is the mixing mechanism that creates the bubble-particle interactions. It consists of a rotor attached to a shaft driven by an electric motor. As the rotor operates, it sucks the slurry from the bottom of the cell and disperses it to the stator blades and out toward the edges of the cell.
Higher-volume cells mean greater efficiency
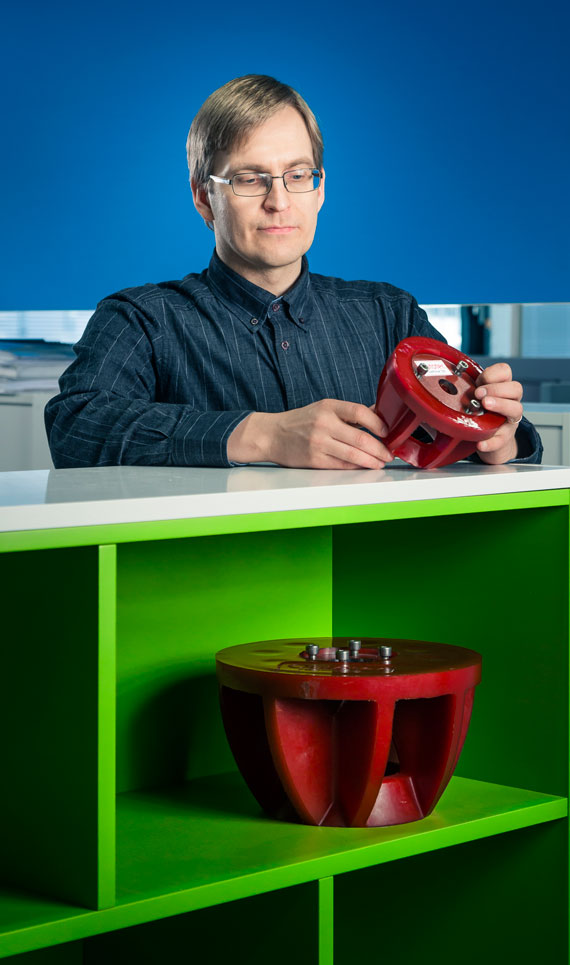
Flotation's sustainable future“As ore grades continue to decline, producers have to process greater volumes of ores to achieve the same returns. At the same time, increasing pressure to reduce their carbon footprint has led them to seek out ways to improve the energy efficiency of their flotation processes and the sustainability of their overall operations,” says Jarmo Lohilahti, Technology Manager, Flotation.
“Larger-volume flotation cells bring the benefit of lower energy consumption per cubic meter of material processed, and allow for a simpler plant layout with a smaller overall physical footprint. Using fewer, larger units also means substantial savings in construction costs, auxiliary equipment, and maintenance,” he continues.
A large flotation plant can have a total operating power of several megawatts, and the direct investment cost of a large flotation cell is approximately only one tenth of its energy costs over a typical lifecycle of 25 years. Cell size is also important: the energy consumption of a 100-m³ cell compared to a 300-m³ cell is approximately 20–30 percent higher. From these figures it is easy to see that scaling up the size of equipment and improving its energy efficiency can have a significant impact on both sustainability and profitability.
Outotec’s R&D efforts focus on improving the sustainability of the flotation process both by developing cells with increasingly larger volumes and on optimizing the electricity consumption of the mixing mechanisms that power them.
After launching what was the world’s largest flotation cell in 2007, the TankCell® e300, with an effective volume of over 300m³, Outotec introduced the TankCell e500 in 2012 and commissioned it in 2014 at First Quantum Minerals’ Kevitsa mine in Finland. It is designed for projects with high material throughputs, such as large copper and gold operations. The metallurgical evaluation of e500 was done in different process conditions and varying the operational parameters. Based on the test campaign, the e500 consumes 20-25 percent less specific energy (kW/hm3) than TankCell® e300 would do in similar conditions. In 2014, we introduced the groundbreaking e630, which with an effective volume of 630 m³ is once again the world’s largest flotation cell.
Reducing energy consumption
The Outotec FloatForce® mixing mechanism enables more efficient pumping of slurry inside the flotation tank. This improved pumping performance means that the rotation speed of the mechanism can be reduced without affecting performance, which in turn reduces power consumption and component wear.
By replacing the existing mixing mechanism with FloatForce, producers can improve both the sustainability and the metallurgical performance of their flotation process: reduced power consumption translates into a smaller carbon footprint, while more efficient pumping, improved air dispersion, and the improved recovery of coarse particles enables better recovery. Existing cells can be retrofitted with a custom-designed mechanism that has a smaller rotor diameter or a lower tip speed to improve energy efficiency.
“Supporting customers with existing installations is a very important part of our handprint, helping them achieve their sustainability and productivity targets,” Lohilahti points out. “Flotation is a very demanding process in terms of energy consumption, so even small gains in efficiency can make a big difference to the sustainability of an operation,” he concludes.
Maximizing our handprint
• Larger-volume flotation cells consume less energy per cubic meter of material processed
• They also allow for a simpler plant layout with a smaller overall physical footprint
• Outotec FloatForce®’s slower rotation speed reduces power consumption and carbon footprint while enabling better recovery levels
Source: http://www.outotec.com/en/Sustainability/Cases/Flotations-sustainable-future/
![]() |
Field Service Representative
To provide field advisory services for customers on existing and/or newly acquired equipment and components.
Operational Purchaser
As Operational Purchaser you will be responsible for assigned purchase order processing and inbound process monitoring related tasks in the Customer Logistics organization for North & Central America.
Field Service Technician
We are now looking for one Field Service Engineer for Automation/Analysers to join the Service team in Canada.
The position is based in Canada to support customers across the country.